A Fair Comparison Between Biomedical Service Providers
MISTAKE #1
Choosing the Right Service Provider Meaning
- Having a fair comparison between the two or more service providers
- Comparing the services that can be compared with each other
- Finding the difference between the services provided
How can you tell if one company is any better or any worse, or any different from another?
How do you know who to contract without being an expert yourself? This section will help you answer important questions – and ultimately save you time, money, worries, and stress by showing you how to find the right biomedical service provider whether you a healthcare professional, a medical equipment manager, or supplier of medical devices.
The Bottom Line
To ensure a hassle-free experience with the servicing of your medical equipment, you should do some detective work on any service provider you’re considering to contract. Use this checklist as a guide. Taking the time to complete the checklist can save you thousands of dollars…. LITERALLY!
MISTAKE #2 TOP
Choosing a service provider who is not supported by the major suppliers and brands of medical equipment.
The major manufacturers and suppliers, actively seek out the premier biomedical service providers because they want to be confident that their service reputation is protected. They want to ensure that their customers are provided with the service they expect, that will ultimately assist to deliver reliable equipment and a high level of patient care.
- Maintaining relationships with multiple service providers is an expensive business that adds to overheads and eats into administrative and training time.
- For medical professionals, the most critical pieces of equipment in their practice are the medical devices used for clinical analysis and treatment of their patients, as well as equipment used for sterilisation of surgical instruments, such as their autoclaves and instrument washers. Without these, you simply can’t operate. If you own or are responsible for the operation of a medical practice, you probably have installed a number of different brands over the years. To minimise the downtime when things go wrong, you need to use a service contractor that has been appointed by the majority of manufacturers and suppliers to support their products. Having a strong relationship with suppliers guarantees the use of genuine spare parts and professional technical support as needed.
- This will help to cut costs by having one company validate and service all of your medical equipment, minimises call out fees, and the amount of billable hours required to keep all your medical devices and autoclaves in optimal working conditions. You also save by ensuring parts are sourced from the original manufacturer without additional and costly margins being applied.
- Also downtime is minimised as you are less likely to have to wait days for parts.
- Make sure you select a service provider who can demonstrate that the majority of manufacturers in Australia have entrusted them to protect their most valuable assets, and their brand.
- If your service provider measures up against the manufacturer’s requirements, the chances are that they will look after you and provide the service levels you are expecting.
MISTAKE #3 TOP
Choosing a service provider who can’t afford to keep an extensive inventory of spare parts
- Maintaining a comprehensive range of spare parts for a range of medical devices and autoclaves requires significant capital. You’d be surprised how many sub-contractors cut back in this area.
- Low spare parts stock means that the technician is often scratching around in the back of his van looking for any part that might get you out of trouble. We’ve even seen repairs that use rubber bands, electrical tape, wrong sealants, or glue, for a temporary fix, because the correct manufacturer’s parts were not available to the technician. Some technicians will even fit a used part they took out of somebody else’s machine.
- Nobody ever thinks to question a potential service provider about their spare parts inventory levels. This will affect the rapid response and turnaround time on repairs.
- Make sure you don’t make this mistake and ask some probing questions about spare parts inventory levels when selecting a service contractor
MISTAKE #4 TOP
Choosing a Service provider who does not have an extensive holding of loan equipment.
- When you have a busy surgery, you need to have confidence that if a machine cannot be repaired promptly that the service provider backs up the service with an extensive holding of loan equipment. If, for some reason, your machine needs to be taken back to the workshop for repair, and the service provider does not provide this additional level of support, you may be exposed to a significantly enhanced risk of economic loss due to extended downtime.
- Another time you may need to depend on loan equipment is when your machine is deemed uneconomic to repair and there may be a delay in obtaining a replacement.
- Receiving loan equipment lets you continue to provide normal services without interruption.
- Ask any potential service provider, questions about how many devices they have available for loan. By doing this, you can easily avoid making this mistake.
MISTAKE #5 TOP
Not leveraging economies of scale by failing to negotiate group contract for multiple sites.
- Let’s face It’s easy to overlook service arrangements on autoclaves and other medical equipment until something breaks down. When you are in a crisis, facing the stress of downtime, and a looming patient backlog, this is not the time to be making decisions about who services your equipment. As a result, service arrangements in a large network of surgeries are often developed on an ad-hoc, as needed basis. When faced with urgent call outs, fees become inflated and that leads to increased servicing costs.
- By choosing a major service provider who recognises the value of your network, you can negotiate a group solution to your service needs. Establishing an annual service/maintenance contract for all of your healthcare facility under one contract will have cost and priority service benefits. U-Tech Medical can provide wide coverage with technical support across Australia. Not all service providers have this level of geographic coverage.
- Another benefit of negotiating a single corporate service contract is that you will also receive priority service. This means that when you have an equipment failure and need urgent technical support, you are not left waiting in a queue of scheduled service calls waiting your turn. Instead, your call will be escalated to the top of the queue. This means that the very next available technician will be dispatched to your call.
- So by avoiding this mistake and selecting an appropriately qualified service provider with extensive geographic coverage, you not only reduce costs, but you also reduce the amount of downtime.
MISTAKE #6 TOP
Not choosing a service provider who provides online access to automated and self-serve reporting.
- In this connected world, you need a service provider who provides you with a client portal that enables you to log jobs and see status lists of equipment your service provider is managing. If your service provider can’t provide this to you, and you would like this service than look for another company.
- When you have a large number of affiliate or branch offices, you have an even greater demand for information as there are an increasing number of stakeholders that need to be kept informed about service priorities and maintenance. In this case, you need to ensure that your biomedical service provider can provide automated scheduled reporting that is customised to meet your requirements and access to an online system that allows you to produce ad-hoc reports as required so that you always have the information you need at your fingertips to answer the questions that arise across your network.
MISTAKE #7 TOP
Not choosing a service provider who provides online access to automated and self-serve reporting.
- In this connected world, you need a service contractor who can provide you with a client portal that enables you to log service jobs, and see service status of your equipment, live and at your convenience. If your contractor can’t provide this feature, you will need to wait for normal business hours to have your questions answered.
- When you have a large number of clinics or branches, you have an even greater demand for information as there are an increasing number of stakeholders that need to be kept informed. In this case, you need to ensure that your biomedical service provider can provide automated or online scheduled reporting that is customised to meet your requirements. Access to an online system allows you to produce status reports as required so that you always have the information you need at your fingertips to answer the questions that arise across your network.
MISTAKE #8 TOP
We meet people that are not aware of the many standards that could apply to their medical facility and simply test medical equipment in their routine electrical test and tag program under AS 3760.
- This is NOT sufficient to be compliant when servicing medical To comply with the standards relevant in our circumstances, the technician you appoint must have received appropriate training and have access to the necessary specialist biomedical test equipment and follow the manufacturer’s test procedures using properly calibrated test equipment.
- In most circumstances, the standards require that medical equipment and autoclaves undergo acceptance, performance qualification and safety testing before new equipment is released for clinical Acceptance testing encompasses a set of administrative and technical processes that must be performed.
- During acceptance testing, a preventative maintenance schedule is developed for the equipment that defines service intervals according to prescribed criteria that are designed to reduce the probability of failure or degradation in performance.
- Standards compliance is particularly important in today’s litigious society where the chain of responsibility comes under critical examination in the case of a workplace incident involving medical equipment. Typically in these cases, the first matter to be examined is standards compliance. If this cannot be demonstrated beyond reasonable doubt, the owner of the equipment in question faces significant exposure to litigation and adverse
- If you are working within an ISO9001 Quality Assurance framework, failure to comply with the relevant standards can result in a Non-Conformance. This may result in significant expense to rectify if there is a backlog of equipment to test at one time if an unsatisfactory compliance audit is
- Don’t make this mistake, ensure that your service technicians are fully aware of the requirements of the various standards and can demonstrate to your satisfaction that they have the necessary training and test equipment that demonstrates If in doubt, ask them about how they comply with the standard. If you are not satisfied with their answers, don’t engage them and seek an alternative complying service provider.
The Australian Standards requires that all medical equipment must undertake routine testing by a qualified biomedical technician during its service life, in order to ensure its continued safety and performance. This is quite a complex area so the following is a table that will help you understand what standards are applicable in your particular circumstances.
Standard | Standard Title | Medical Centres, Day Surgeries and Hospitals | Dental Practices | Physiotherapy Practices | Pre-Post Hospital, Occupational health, Life Saving organisations medical education, industrial, home care markets |
AS3003 | Electrical installations - Patient treatment areas of hospitals and medical and dental practice | Yes | Yes | Yes | Yes |
AS3551 | Management programs for medical equipment | Yes | Yes | Yes | Yes |
AS3840 | Pressure regulators for use with medical gases. Pressure regulators and pressure regulators with flow-metering devices | Yes | Yes | Yes | |
AS3760 | In-service safety inspection and testing of electrical equipment | Yes | Yes | Yes | Yes |
AS4815 AS4187 | Cleaning, disinfecting and sterilising reusable medical and surgical instruments and equipment, and maintenance of associated environments in health care facilities | Yes | Yes |
MISTAKE #9 TOP
Inadequate insurances held by a contractor could leave you exposed to litigation if a workplace incident occurs.
- There are additional underwriting risks insurers face when providing liability insurance to medical service engineer so ordinary public liability cover is not sufficient. Service providers need to take out specific insurances. Make sure the service provider you select holds specialist Medical Equipment Product & Public Liability insurance with at least $20 million cover.
- You should also ensure that your service provider holds Work Cover Insurance for all Ask to see a copy of their current insurance policies to avoid making this mistake.
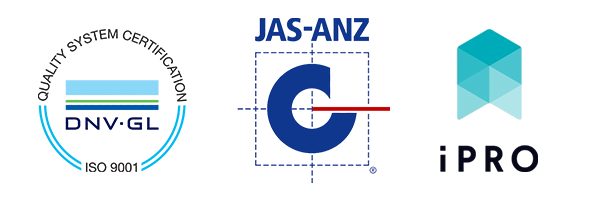
U-Tech Medical is ISO 9001:2015 certified, iPRO Smartek and JAS-ANZ certified.
ISO 9001 2015 is the world’s most widely recognised Quality Management System. This means you are employing the world’s best practice methods, policies and procedures, it helps dental practitioners to meet the expectations and needs of their patients